Los cinco ¿Por qué? Índice Ejemplo Historia Técnicas Crítica Véase también Referencias Menú de...
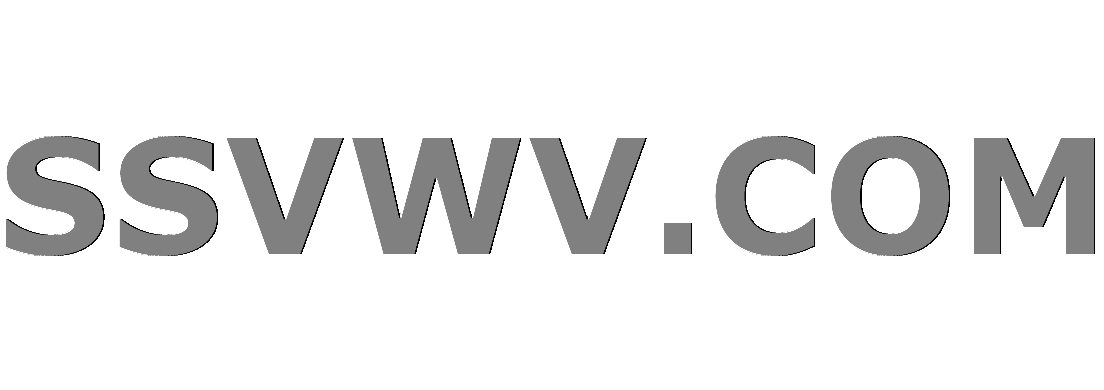
Multi tool use
CalidadSolución de problemas
técnicaiterativascausa y efectocausa raízdefectoSakichi ToyodaToyotaRicardo SemlerSemcoiteracionesSakichi Toyoda (en inglés)Toyotasistema de producción Toyotasistema de producción ToyotaTaiichi OhnoKaizenmanufactura esbeltaSix Sigmaespina de pescado (o diagrama Ishikawa)causas raízToyotacausa raízcondición necesaria y suficiente
Los 5 ¿Por qué? es una técnica para realizar preguntas iterativas, usadas para explorar las relaciones de causa y efecto subyacentes a un problema particular.[1] El objetivo principal de la técnica es determinar la causa raíz de un defecto o problema repitiendo la pregunta "¿Por qué?". Cada respuesta forma la base de la siguiente pregunta. El "5" en el nombre se deriva de la observación empírica en el número de iteraciones típicamente requeridas para resolver el problema.
La técnica fue originalmente desarrollada por Sakichi Toyoda y fue usada en la corporación de motores Toyota durante la evolución de su metodología de manufacturación. En otras compañías esta técnica aparece en otras formas. Bajo la dirección de Ricardo Semler, Semco utiliza tres "¿Por qué?" y amplía la práctica para la determinación de metas y la toma de decisiones.[2]
No todos los problemas tienen una sola causa raíz si uno desea descubrir múltiples causas raíces, el método debe ser repetidos, preguntando una secuencia diferente de pregunta cada vez.
El método no provee reglas sencillas ni estrictas acerca de que líneas de preguntas hay que explorar o que tan largo seguir la búsqueda de causas principales adicionales. Por consiguiente incluso cuando el método es cuidadosamente aplicado el resultado sigue dependiendo del conocimiento y la persistencia de las personas involucradas.
Índice
1 Ejemplo
2 Historia
3 Técnicas
4 Crítica
5 Véase también
6 Referencias
Ejemplo
- El vehículo no arranca. (El problema)
¿Por qué? - La batería está muerta. (Primer ¿por qué?)
¿Por qué? - El alternador no está funcionando. (Segundo ¿por qué?)
¿Por qué? - La correa del alternador se ha roto. (Tercer ¿por qué?)
¿Por qué? - La correa del alternador fue mucho más allá de su vida de servicio útil y no se ha sustituido. (Cuarto ¿por qué?)
¿Por qué? - El vehículo no se mantiene de acuerdo al recomendado programa de servicio. (Quinto ¿Por qué?, una de las causas)
El cuestionamiento de este ejemplo podría profundizarse a un sexto, séptima, o de nivel superior, pero cinco iteraciones de preguntar por qué es generalmente es suficiente para llegar a una de las causas. La clave es fomentar el solucionador de problemas para evitar suposiciones y trampas lógicas y en su lugar rastrear la cadena de causalidad en incrementos directos del efecto a través de cualquiera de las capas de abstracción a una de las causas que todavía tiene algo de conexión con el problema original. Tenga en cuenta que, en este ejemplo, el quinto qué sugiere un proceso roto o un comportamiento alterable, que es indicativo de alcanzar el nivel de la causa raíz.
Es interesante notar que la última respuesta apunta a un proceso. Este es uno de los aspectos más importantes de la técnica de los "5 porqué" la causa raíz real debe apuntar hacia un proceso que no está funcionando bien o no existe.[3] Facilitadores no capacitados a menudo observa que respuestas parecen apuntar hacia respuestas clásicas como no hay suficiente tiempo, no hay suficientes inversiones, o no hay suficiente mano de obra. Estas respuestas pueden ser ciertas, pero están fuera de nuestro control. Por lo tanto, en lugar de hacer la pregunta ¿Por qué?, se puede hacer la pregunta ¿Por qué fallo el proceso?.
Una frase clave a tener en cuenta en cualquier ejercicios de 5 ¿Por qué? "los procesos no fallan, las personas sí".
Historia
La técnica fue originalmente desarrollada por Sakichi Toyoda (en inglés) y fue usada dentro de Toyota Motor Corporation durante la evolución de sus metodologías de fabricación. Es un componente crítico del entrenamiento a la resolución de problemas, impartido como parte de la inducción en el sistema de producción Toyota. El arquitecto del sistema de producción Toyota, Taiichi Ohno, describió el método de los 5 ¿Por qué? como las bases de un enfoque científico de Toyota… mediante la repetición de los 5 porqués, la naturaleza del problema así como su solución se hace clara.[4] La herramienta ha tenido un uso extendido más allá de Toyota, y ahora es usada dentro de Kaizen, manufactura esbelta y Six Sigma.
Técnicas
Existen dos técnicas primarias que se utilizan para llevar a cabo 5 ¿Por qué?:[5] el diagrama de espina de pescado (o diagrama Ishikawa) y un formato tabular.[6] Estas herramientas permiten que el análisis se ramifique con el fin de proporcionar múltiples causas raíz.
Crítica
Mientras los 5 ¿por qué? es una poderosa herramienta para ayudar a ingenieros o individuos experimentados con esta técnica para encontrar la verdadera causa de los problemas, esto ha sido criticado por Teruyuki Minoura, ex gerente director de adquisiciones globales de Toyota, por ser una herramienta demasiado básica para analizar el origen de la causa raíz requerida para asegurar que estas sean reparadas.[7] Algunas razones para esta crítica:
- Tendencia de los investigadores de detenerse en los síntomas antes de ir al nivel más bajo del origen de las causas.
- Incapacidad de los investigadores de ir más allá de los actuales conocimientos no poder encontrar las causas que ellos no conocen.
- Falta de soporte para ayudar a los investigadores al preguntarse el correcto “por qué” de las preguntas.
- Resultados no son repetibles: diferentes personas que usan “Los 5 ¿Por qué?” obtienen diferentes causas para el mismo problema.
- Tendencia de aislar una sola causa raíz cuando cada pregunta podría enumerar muchas diferentes causas verdaderas.
Estos pueden ser los problemas significantes si la técnica es aplicada solamente a través de la deducción. Es recomendable, hacer una verificación inmediata a la respuesta de la pregunta "¿Por qué?" actual, antes de proceder a la siguiente, para evitar estos problemas. Además pruebas lógicas para la condición necesaria y suficiente en cada nivel puede ayudar a evitar la selección de causas falsas y promover la consideración de múltiples causas raíz.[8]
Véase también
- Causalidad
- Ocho disciplinas para la resolución de problemas
Cinco W (recopilación de información)- Método socrático
- Sistema de producción Toyota
- Monozukuri
- Lean manufacturing
Referencias
↑ «Five Whys Technique». adb.org. Asian Development Bank. February 2009. Consultado el 26 de marzo de 2012.
↑ Semler, Ricardo (2004). The Seven-Day Weekend. Penguin. ISBN 9781101216200. «Ask why. Ask it all the time, ask it any day, and always ask it three times in a row.»
↑ Ivan Fantin (2014). Applied Problem Solving. Method, Applications, Root Causes, Countermeasures, Poka-Yoke and A3. How to make things happen to solve problems. Milan, Italy: Createspace, an Amazon company. ISBN 978-1499122282
↑ Taiichi Ohno; foreword by Norman Bodek (1988). Toyota production system: beyond large-scale production. Portland, Or: Productivity Press. ISBN 0-915299-14-3.
↑ «An Introduction to 5-why». Consultado el 6 de marzo de 2010.
↑ «5-why Analysis using an Excel Spreadsheet Table». Consultado el 25 de diciembre de 2010.
↑ «The "Thinking" Production System: TPS as a winning strategy for developing people in the global manufacturing environment». Archivado desde el original el 27 de febrero de 2014. Consultado el 19 de febrero de 2014.
↑ Wilson, Bill. «Five-by-Five Whys». http://www.bill-wilson.net. Consultado el 7 de octubre de 2014.
F7rZtQg